Inspecting an as-built bridge abutment with PIX4Dcatch
Ai Consultant, based in Tokushima Prefecture, was commissioned by Sasaki Corporation in Awa City to perform control measurements of bridge abutment foundation work (cast-in-place piles). The site's conditions made traditional stationary surveying instruments inefficient for measurements, so a case study was conducted to see if the problem could be solved with PIX4Dcatch and mobile 3D scanning. We interviewed Mr. Kirai, CEO of Ai Consultant, who oversaw the case study.
Key takeaways
- PIX4Dcatch enabled efficient as-built inspection while ensuring the required measurement accuracy;
- PIX4Dcatch outperformed other mobile measurement technologies in terms of repeatability and accuracy.
Tell us more about the case study
The construction site was surrounded by a mountain slope in the back and an irrigation canal in the front, which restricted the space for a laser scanner and/ or other equipment. The pile-head rebar was a blind spot and an obstacle for measuring, which made it inefficient to use this stationary and more traditional measurement equipment.
To address this issue, two types of 3D mobile measurement techniques were used to collect data while walking. The first was PIX4Dcatch. PIX4Dcatch generates point clouds from photogrammetry and uses the mobile device’s LiDAR, which can then be processed by PIX4Dmatic, or the online platform PIX4Dcloud.
The other mobile measurement device was a LiDAR-only solution, Solution P. We focused on the three elements of the as-built inspection management standard, i.e., reference height, eccentricity, and pile diameter, and then did a comparison across 3 methods:
- Traditional stationary surveying equipment
- PIX4Dcatch
- Solution P
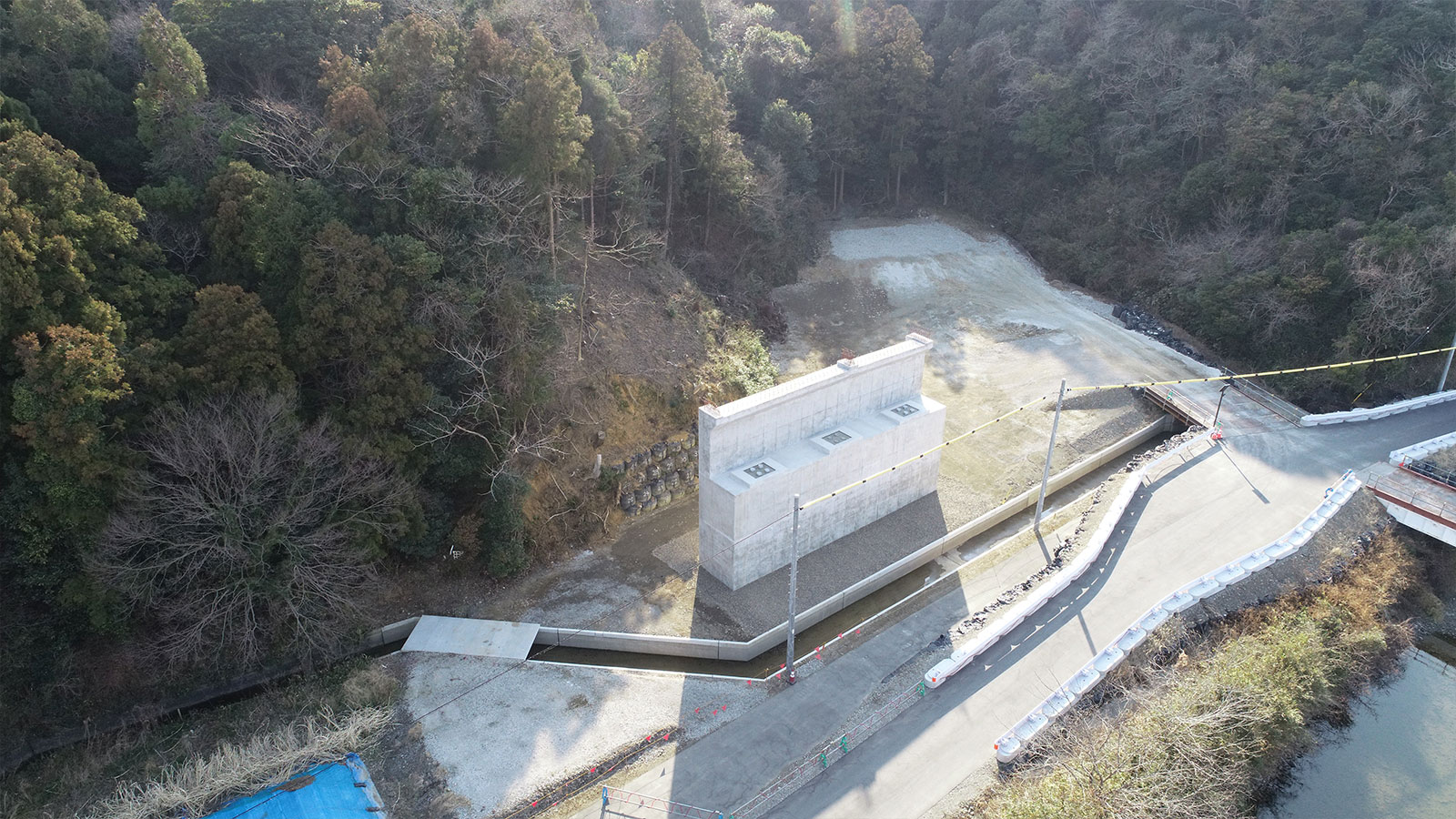
How PIX4Dcatch was used:
The target was 18 piles of bridge abutments, and an area of approximately 8.8x16.1 meters was photographed in triplicate. The data was collected using PIX4Dcatch and an app from Solution P, respectively.
The data collected with PIX4Dcatch was analyzed and processed with PIX4Dmatic. PIX4Dcatch uses both image and LiDAR data to make a denser, high-quality point cloud. We used PIX4Dcatch without an RTK rover. Since the output point cloud didn’t contain the coordinates of the world geodetic system, we used the grading points measured by the total station for the coordinate transformation and aligned the point cloud accordingly.
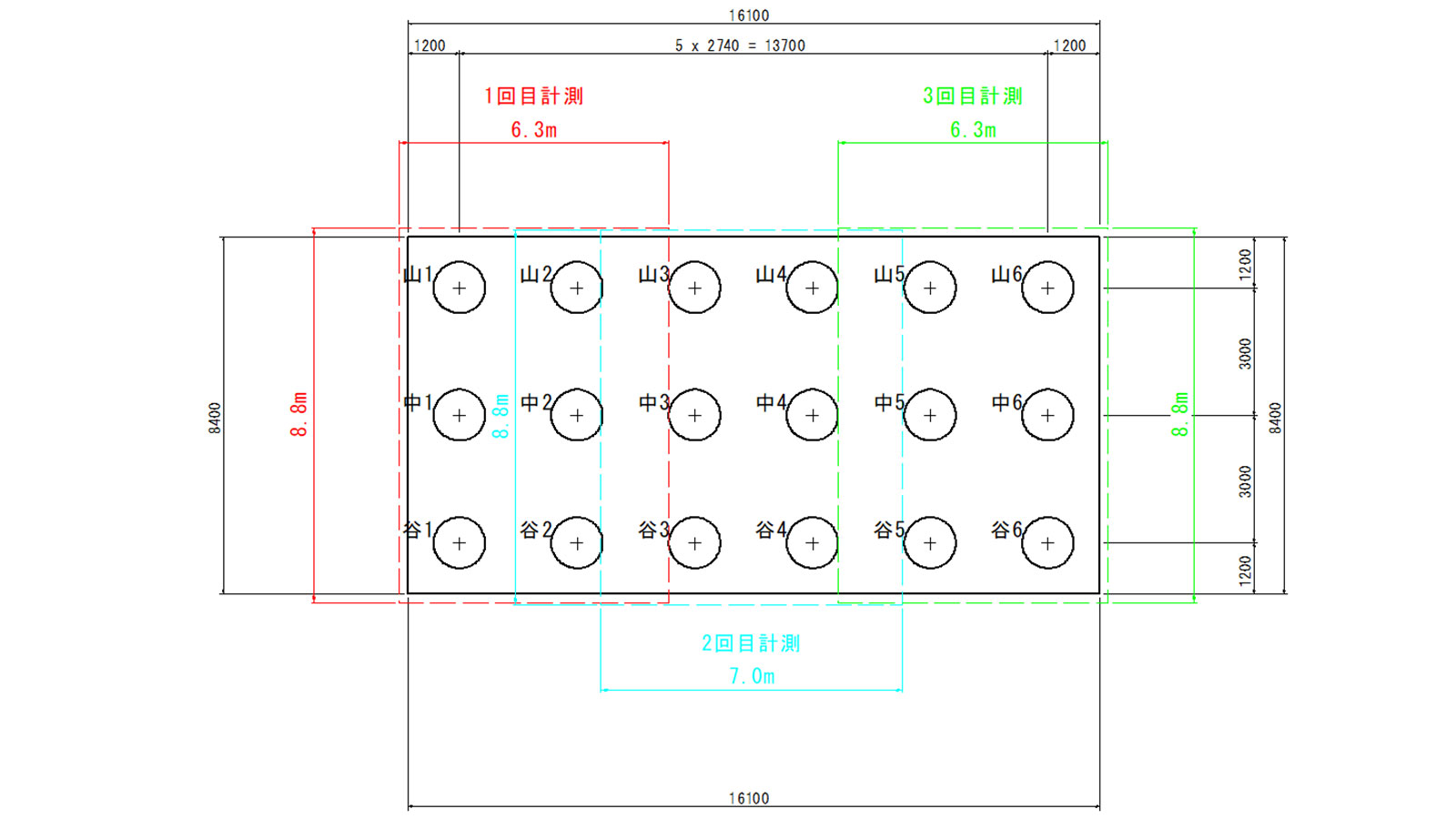
Project details
Location | Awa City, Tokushima Prefecture, Japan |
User | Ai Consultant |
Software used | PIX4Dcatch PIX4Dmatic |
Hardware used | iPad Pro 2020 11 inch Wi-Fi 128GB Workstation: Windows10 OS,Intel(R) Xeon(R) CPU E5-2687W v3 @ 3.10GHz. RAM: 64.0GB, GPU:Quadro K5200 |
Captured area | 135.24m2 as a whole (divided into 3 areas) |
Number of images | Area 1: 2,427 Area 2: 2,699 Area 3: 1,842 |
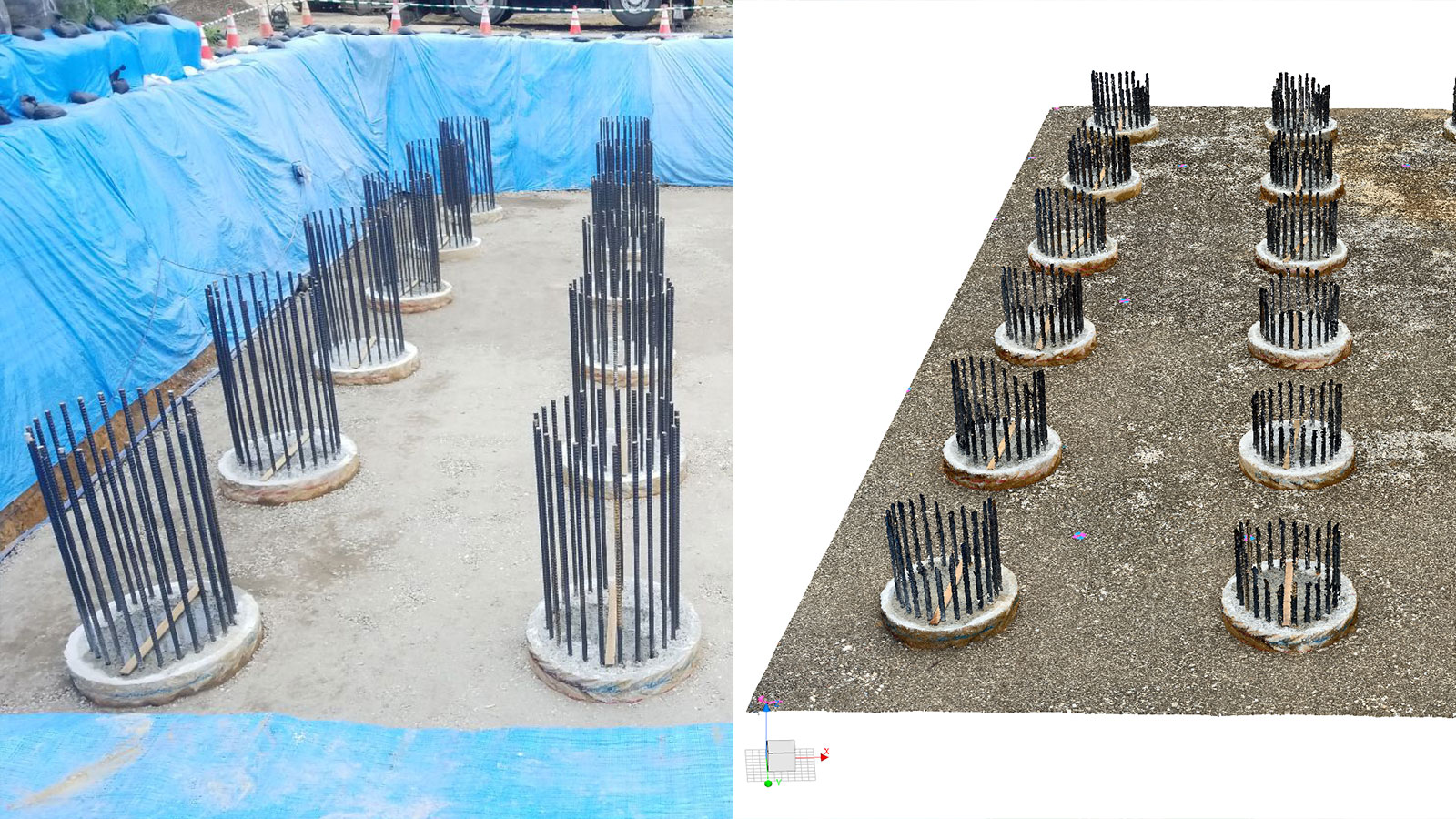
Results: how did PIX4Dcatch compare with conventional technology?
By using PIX4Dcatch we were able to overcome the unfavorable, restrictive conditions of the site. The results from PIX4Dcatch showed that the measurements of the base height, eccentricity, and pile diameter met the prescribed standard values specified in as-built management guidelines.
Standard height: within ±50mm of the design value Eccentricity: within 100mm Pile diameter: Design value -30mm or more
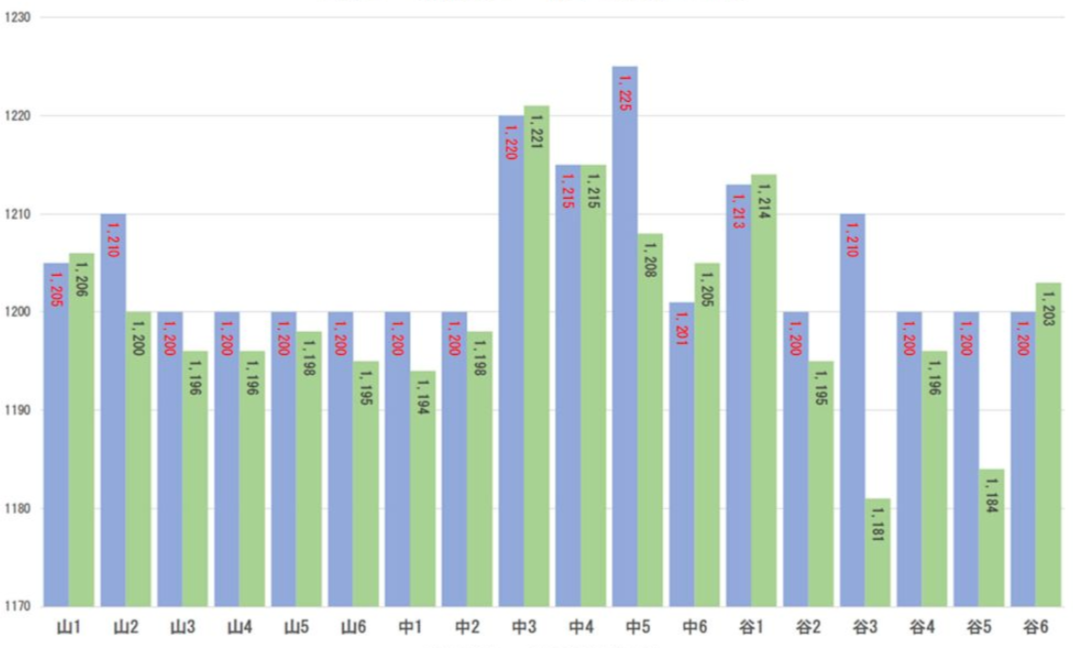
In addition, the time required for data acquisition on-site was significantly reduced and productivity improved using PIX4Dcatch. With mobile scanning the measurements were completed by one person in approximately 5 minutes x 3 times = 15 minutes in total!
With conventional equipment it took two people approximately 7 hours to complete measurements and create control charters. With PIX4Dcatch, using the high-density point cloud, one person spent just over two hours calculating the semi automatic control values. Since the calculation was semi-automatic it reduced dependency on differing levels of skills and experience, thus standardizing the quality and outcome of the work.
“We feel that PIX4Dcatch has great potential as a tool for terrestrial surveying that can create accurate point cloud models. We would like to use it to take on the challenge of solving issues at the site in addition to the foundation work we worked on this time." - Mr. Kirai, Representative Director of Ai Consultant
We processed the image data from PIX4Dcatch using PIX4Dmatic. With PIX4Dmatic multiple projects can be processed automatically, and processing can be performed in parallel with other work or at night. PIX4Dmatic also has the ability to queue processing, so as soon as one project is processed, the next can automatically start! Since we only used PIX4Dcatch, it took time to convert the coordinates, but if an RTK device was used we would have reduced the work time even further.
How did PIX4Dcatch compare with LiDAR-only mobile scanning?
PIX4Dcatch performed very well in the comparison between the different mobile measurement technologies; even the edges were reproduced clearly, and I was surprised that the rebar was accurately converted into a point cloud.
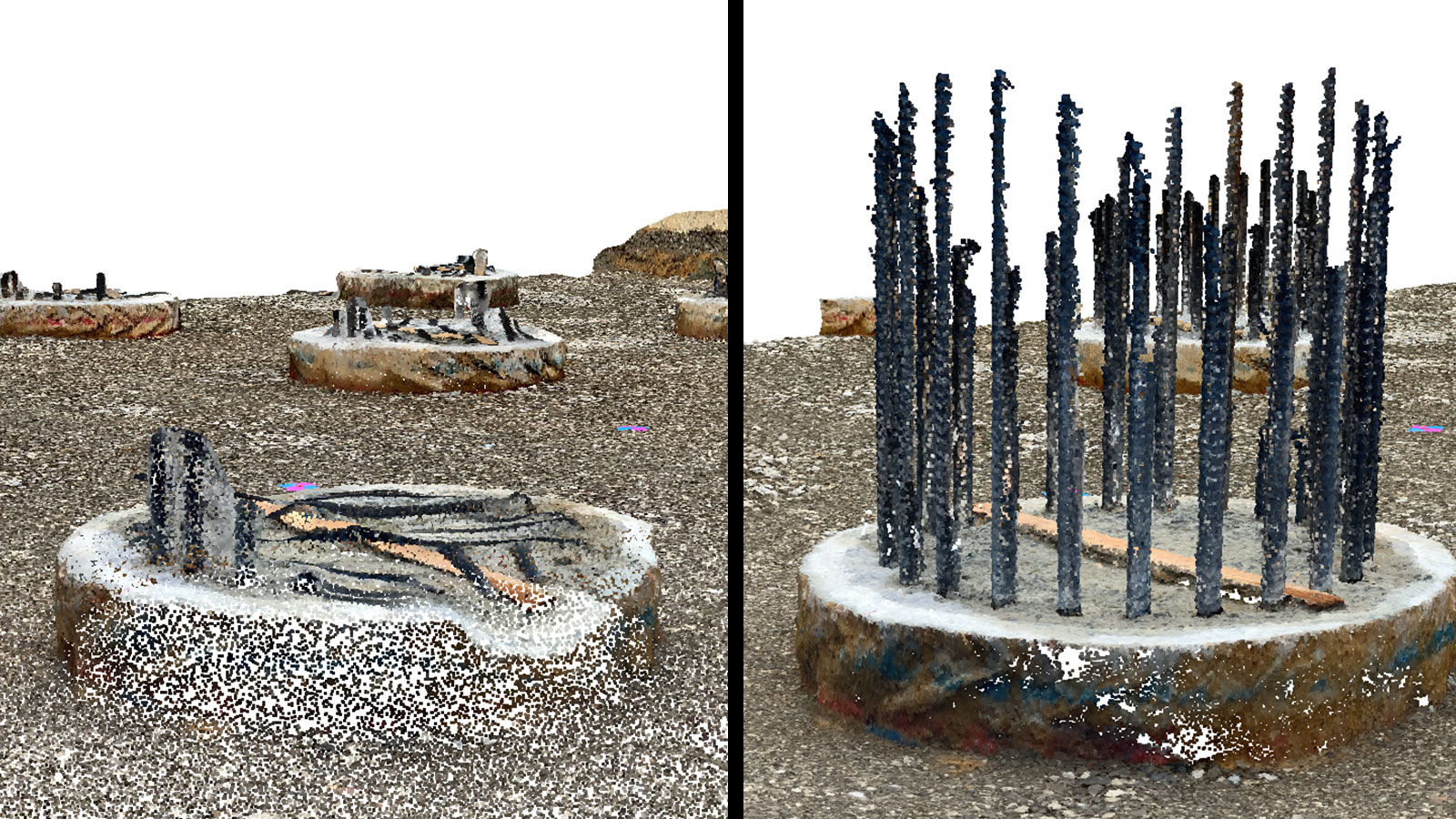
The PIX4Dcatch system met all the requirements for X, Y, Z, measurement density, and satisfied the measurement accuracy specified in the as-built management guidelines.
Accuracy results
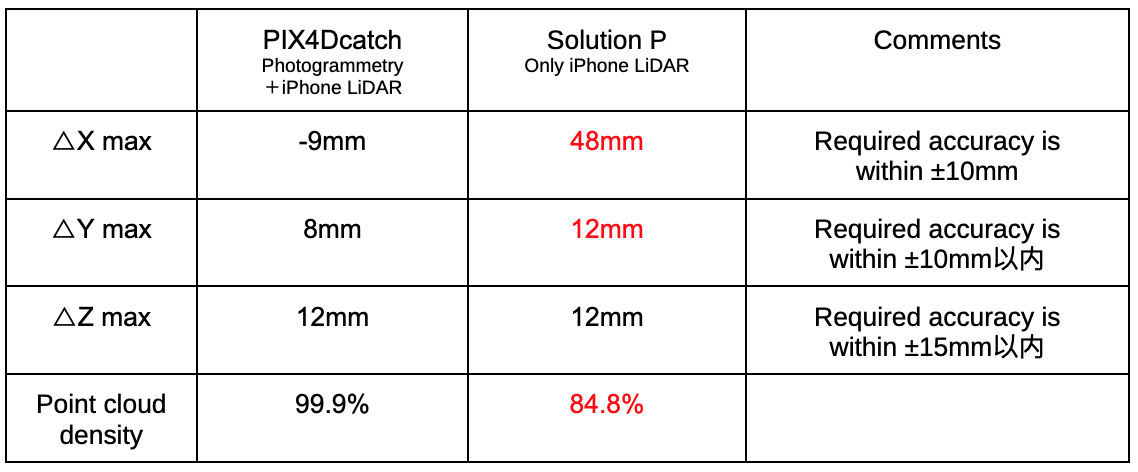
The report was very well received by the client, Sasaki Corporation, who submitted it to the Ministry of Land, Infrastructure, Transport, and Tourism as an initiative of originality and ingenuity. The project was widely introduced at various opportunities, including on-site seminars.
In the end, many of our efforts, including this demonstration, were evaluated highly. The construction of the site in question was nominated by the Tokushima Office of Rivers and National Highways as a safe construction project in 2023, and the supervisory engineer nominated as an excellent construction engineer. Both received an award from the Director General of the Shikoku Regional Development Bureau.
We would like to thank Image One Corporation, a premium reseller, Geosurf Corporation, and Jitsuta Co., Ltd. for their cooperation in preparing this report.